Abstract With the implementation of the new PV on-grid price on January 1, 2017, the on-grid tariffs of China's three types of solar energy resources have come to 0.65, 0.75, 0.85 yuan/kwh, and are closer to parity. Weaning is imperative, how to reduce costs and increase efficiency has become a must for PV companies...
With the implementation of the new PV on-grid price on January 1, 2017, the on-grid tariffs of China's solar energy resource zones have reached 0.65, 0.75, 0.85 yuan/kwh, and are closer to parity. Weaning is imperative, and how to reduce costs and increase efficiency has become a must-have for PV companies. Photovoltaic modules are a key component of power plant operation. The cost of components in photovoltaic power plant investment accounts for about 45%, and the decline in component costs will drive down the overall cost of photovoltaic systems. According to industry estimates, the cost of photovoltaic modules will drop by 0.1 yuan for every 10 yuan reduction in PV module costs. The increase in component efficiency will directly bring more power generation to the photovoltaic power station and increase the revenue of the power station owners.
Therefore, PV modules have become the main link of cost reduction and efficiency improvement of photovoltaic power generation, and component companies have been fighting for cost efficiency. Among them, the monopoly of crystalline silicon components is the main competition.
æ–© Constant single polycrystalline battle
Crystalline silicon is the most important photovoltaic material for solar energy utilization. When the molten elemental silicon solidifies, the silicon atoms are arranged in a diamond lattice into a plurality of crystal nuclei, such as crystal grains having the same crystal orientation as the crystal faces, forming single crystal silicon, and if the crystal nuclei grow into crystal grains with different crystal orientations. , is polysilicon.
In terms of efficiency, single crystal silicon solar cells have high photoelectric conversion efficiency. From the perspective of production cost, polycrystalline silicon solar materials are easy to manufacture, save power consumption, and have low total cost, so they have been developed on a large scale.
For a long time, the market rate of polycrystalline and single crystal photovoltaic modules has remained at 8:2, which is the result of 35 years of market selection. In the past two years, with the use of diamond wire cutting on single crystals, the cost of single crystal has dropped significantly, and the market balance has been broken.
Some agencies predict that the ratio of single and polycrystalline market in 2017 will be changed to 4:6. Single crystals reduce costs, and polycrystals are working to increase efficiency. Recently, Trina Solar announced that its HoneyPlus high-efficiency polycrystalline silicon solar module (mc-Si) has a pore size efficiency of 19.86%; Wuxi Suntech has announced that its polycrystalline PERC battery is up to 20% efficient. However, in terms of efficiency, it is still difficult for polycrystalline components to catch up with single crystal components.
In this battle of efficiency costs, industry insiders said that if the price of monocrystalline silicon wafer is less than 12% of the portion of the polycrystalline silicon wafer, single crystal is cost-effective because the single crystal efficiency is higher; if the single crystal is more expensive than polycrystalline 12 Above %, even if the single crystal efficiency is high, it is not cost effective. It is also known as the "0.6 yuan spread" of silicon wafers.
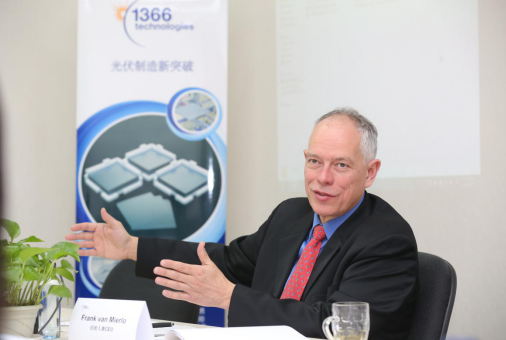
1366 Technology CEO Frank van Mierlo
Therefore, if the efficiency cannot catch up with the single crystal, then maintaining the cost advantage is the layout focus of the polycrystalline enterprise. Direct method silicon wafer cost reduced by 50%
When the manufacturing process is mature, the price reduction of core materials and the reduction in consumption are the main reasons for the continuous price reduction of PV modules.
In the cost structure of photovoltaic modules, silicon wafers account for about 35%-40%. It can be seen that reducing the cost of silicon wafers plays a crucial role in reducing the cost of components and photovoltaic power plant systems. This is also the driving force for polycrystalline to actively promote diamond cutting.
However, the cutting process is always wasteful. It is understood that the traditional silicon wafer manufacturing process needs to first melt, pull or ingot the polycrystalline silicon, then cut into small squares, after grinding, polishing, etc., and finally cut into pieces by wire, which is wasted during the silicon wafer cutting process. Nearly 50% of silicon material, and a large number of steel wire, mortar and other auxiliary materials.
Is there a way to avoid the waste of wafer cutting, which will reduce the cost of wafer production? 1366 technology gives the answer.
According to Frank, 1366 Technology uses direct-method silicon technology to solve this problem. The so-called direct method silicon wafer puts polysilicon into the silicon wafer growth furnace, heats it to melt, and then cools the surface layer and crystallizes it into a polycrystalline silicon wafer, which is like the ice surface of the lake in winter. The wafer is then removed and cut to a specified size at a rate of about 20 seconds per slice, and the cut wafer can be recycled. In this way, the direct method silicon wafer reduces the production steps of silicon ingot casting, cutting, etc., avoids the waste of silicon, can reduce the cost by 50%, and saves two-thirds of the total energy consumption of the entire wafer.
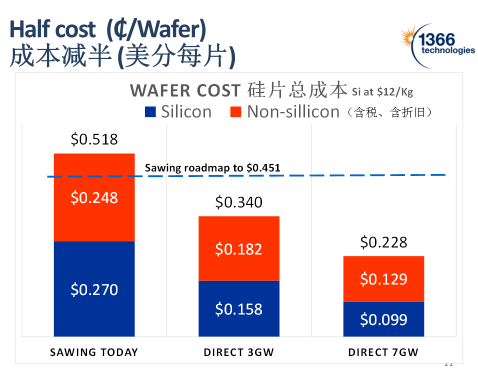
Information from 1366 Technology
As shown in the above figure, the blue line is the cost limit achieved by polycrystalline diamond cutting. 1366 Technology believes that when the output reaches 3GW, the direct method silicon wafer technology can be used, and the silicon cost can reach $0.158/piece. At 7 GW, silicon costs reach $0.099 per piece. Direct-method silicon technology offers a very low-cost option for continuing the dominance of polycrystalline market. In addition, another advantage of the direct method silicon wafer is that the technology can be combined with the PREC technology to achieve a 1+1>2 effect. Not long ago, 1366 Technology and Hanwha QCELLS announced that the cell conversion efficiency of direct silicon technology and Q.ANTUM back passivation battery technology reached 19.6%. Frank expressed confidence that he will achieve the goal of 20% conversion efficiency in Q1 2017.
Frank continued, "When PERC technology is used, if the thickness can be reduced, the use of photons can be more sufficient, but the current process has no way to make the silicon wafer thinner. If it is cut thinner, it will not be worth the loss in the slicing process. - The fragmentation rate of the battery process is too high. The 1366 technology uses 3D grown silicon wafers, which can be thick at the edges and thin in the middle. The whole wafer is also based on 100-200 micron intensity. We give downstream Battery manufacturing offers more possibilities."
After 7 years, 1366 direct-method silicon technology was commercialized and successfully installed in power plants in Germany and the United States. At the end of 2016, half of the 1MW demonstration projects in Japan used direct method wafers.
According to statistics, in 2016, China's photovoltaic grid-connected capacity was about 34.24GW, leading the world for two consecutive years. In Frank's view, China is an important photovoltaic market. 1366 Technology is looking for suitable partners in China to establish a direct silicon wafer factory, together to promote the development of direct silicon wafers, and accelerate the early arrival of affordable Internet access.
Rubber Anti-oxidant Agent is a kind of rubber to join in the process of production can delay the ageing of the rubber, prolonging the service life of the rubber chemicals.
Ningbo Actmix produce the non-staining anti-oxidant for vulcanizates based on natural and synthetic rubbers, included Actmix®MMBI-70, Actmix®MBI-80, Actmix®ZMMBI-50, Actmix®ZMMBI-70, Actmix®NDBC-75 etc, application for variety of transparent,white and colorful rubber products, fabric coating, especially for heat-resistant rubber parts.
Rubber Anti-oxide Agent,Rubber Chemical Anti-oxidizer Agent,Anti-Oxidizer Agent For Rubber,Rubber Anti-oxide
Ningbo Actmix Rubber Chemicals Co., Ltd. , http://www.actmixchemicals.com