The edging is a necessary process in the body-in-white welding process, and is mainly applied to the four-door two-cover and the fender of the automobile body. Generally speaking, when assembling two sheet metal parts, the flange of one part is wrapped around the other part. The edging method can well solve the influence of the solder joints between the inner and outer panels of the door on the appearance, and the door strength can be solved by completely enclosing the inner and outer panels of the door. The edging usually has two implementations of crimping and roll edge. The crimping refers to the traditional mold edging, using a press or some cylinder to drive the pressing block to press the hem, and wrapping the other part to achieve the purpose of assembly; The roll edge is rolled and wrapped around another part by a roller (usually driven by a robotic arm) to achieve assembly.
Robot roll side system introduction
The robot door roll edge system mainly consists of three parts: the roll edge fixture system, the roller system, the robot and its control system and the safety system (see Figure 1).
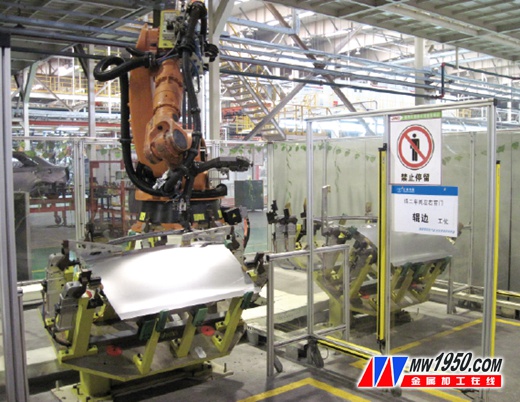
Figure 1 Robot Roller System
Roll edge fixture system
The roll edge clamp system (see Figure 2) is the central area for flexible production using the robot roll edge technology. The system consists of a roll bottom die and a positioning clamp. The bottom mold is machined by integral casting CNC, and its profile is consistent with the profile of the outer panel of the door. Its accuracy directly affects the overall dimensional accuracy of the door. The positioning clamping portion includes positioning clamping of the outer panel of the door and positioning and clamping of the inner panel of the door. The positioning and clamping mechanism of the outer plate member is connected with the bottom mold base, and the outer plate member is preferentially positioned by the hole. If there is no positioning hole on the outer panel, select the shape positioning. When selecting the shape positioning, the position and quantity of the positioning block should be arranged reasonably and fully to ensure that the outer plate member does not move when the partial positioning block is opened during the roll edge process.
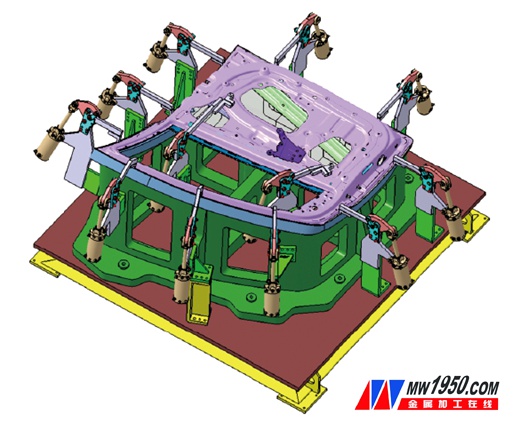
Figure 2 Roller Clamp System
2. Roller system
The roller system is the part of the whole system that is responsible for the hemming and the side of the roll, and is composed of rollers of various shapes. In order to ensure the quality of the edging and improve the appearance quality, the roll edge process is completed in 2 to 4 times. Therefore, the roller is usually designed as a 90° wheel, a 60° wheel, a 30° wheel, a forming wheel and a special special wheel.
3. Robot and its control system
This system is mainly used to control the movement of the roller and the communication between the robot and other related systems. The roll edge process is performed by the robot gripping the roller frame to perform the roll edge program, and the roll edges of the entire door are sequentially completed.
4. Security system
The safety system is used to protect the operator's personal safety. It is mainly composed of a safety grating and a safety scanner. During the normal operation of the robot roller, the operator or foreign matter touches the safety grating, and the robot stops working to avoid injury to personnel.
Tongyue model robot roller side scheme
Roll side step
The Jianghuai Tongyue model has a three-edge process on the side of the door roller. The robot passes the two pre-roll edges and one final roll edge, that is, the roll-edge folding step is 30°→60°→90°, and the flanged sheet is folded. At 180°, the inner and outer plates are wrapped in a flat position.
2. Roller edge entry point
Taking into account the need for beats, the starting point of the roll edge generally starts from the starting point of a more complicated side. In the Tongyue project, the rolling is started from the corner of the window frame and the sharp change of the contour, and finally the rolling is smooth. The desired roll edge condition can be achieved after repeated and repeated rolling, so the end of the last roll pressure is the starting point of the next roll press.
3. Roller pressure
The robot pressure should be adjusted according to the specific conditions (including the complexity of the structure, materials, etc.) (see Figure 3). Generally, the pre-enveloping force is 400-700N for steel and 300-650N for aluminum. The final edge-strength force is 1000-1500N for steel and 900-1250N for aluminum. In order to prevent the expansion and contraction of the plate, the pre-enveloping force should be increased accordingly. In order to avoid the inner plate being extruded, the final wrapping force should be reduced accordingly. If the pressure at the side of the roll is too large, the inner panel of the window frame will be extruded, and the pressure at the side of the roll will be too small to achieve the desired roll edge effect.
Figure 3 shows the pressure at the roll side
4. Roller speed
In theory, the speed of the roll edge can be up to 200mm/s, but the shape of the surface of the plate around the edge of the door is similar, some parts are smooth, and some parts are sharply changed, which is more complicated. Therefore, the actual roll edge speed is inconsistent, the average speed in the smooth zone is 120-150 mm/s, and the speed in the sharp change zone is 50-67 mm/s.
Advantages of the roll edge process
Through the production verification on the Tongyue model, the robot roll side station has the following effects:
(1) High flexibility The running track of the roller side is controlled by the robot program, so only the robot program and the corresponding roll edge fixture system need to be replaced when the model is replaced. Therefore, in theory, a set of robot roller edge system can complete the door pressing and edging process of various models. At present, considering the beat factor, a set of robot roll side systems in the Tongyue project realizes two door roller edges.
(2) One-time investment is small Compared with the investment of the door trimming machine, the investment in the roll-side workstation is less than half of the investment in the edge wrapping machine.
(3) Small footprint The area of ​​the roller-side workstation is very small, which is only equivalent to 14.9% of the area of ​​the door wrapping machine.
(4) Short commissioning period From the end of the installation and commissioning of the robot roll side station to the completion of the process commissioning, the whole process is very smooth, taking less than 4 months, and reducing the commissioning time of the pressure package by 3 months.
(5) Beautiful appearance The outer surface of the door and window frame that comes out of the robot roller is smooth and smooth, without defects such as indentation, depression, convex hull, etc., and the overall strength and rigidity of the door are enhanced.
(6) Saving labor cost The robot roll side workstation can complete four-door roll side work with only two people, while the press machine requires four people. In contrast, the robot roll side workstation saves human resource costs.
(7) The low maintenance cost of the robot is only 13.5 kW, which is less than half of the edge press, and it is also possible to realize one robot simultaneously completing the roll edges of the two doors, so the cost of use is lower than that of the edge press. a lot of. At the same time, the structure is simple, there is no particularly complicated structure, unlike the press, which often needs lubrication, replacement of wearing parts, etc., so its daily maintenance is also very simple and economical, saving maintenance and operation costs of 232,800 yuan per year.
(8) Comfortable working environment The robot roll side workstation basically does not generate any noise, so the operating environment on the site is more comfortable and improves the satisfaction of employees.
Conclusion
As the roll edge technology becomes more and more mature, more auto manufacturers will use the roll edge process to achieve the edge. Whether it is on a truck or a car, the roll edge process has shown its strong competitiveness, and the roll edge process will become the development direction of the future edge wrapping process.
An evacuated tube
is two glass tubes, one within the other, joined at each end. The space between
these tubes is evacuated so the space is under a vacuum seal. Vacuums are
excellent insulators (think thermos.) The inner tube is coated with a selective
coating that converts light into heat.
Guaranteed for
fifteen years (the longest warranty on the market) Linuo tubes are made from
high quality borosilicate glass and are fused together. This provides an all
glass seal. The Linuo evacuated tube uses a unique three layer selective
coating instead of the standard single al-n/al coating. It consists of an
infrared emission layer, an absorption layer and an anti-reflective layer,
giving a much improved performance.
All Glass Evacuated Tube 58-1800mm
glass tube, vacuum tube, evacuated tube, vacuum tube with selective coating, evacuated tube with selective coating
Linuo Ritter International Co.,Ltd , https://www.lnrtsolarenergy.com