With the development of society, the problem of reinforcement and reconstruction of old buildings has become increasingly prominent. In order to save costs, increase the use of space and facilitate residents. New reinforcement scheme: carbon fiber reinforcement.
1-1-2-1 surface treatment 13611272094 (Hugong)
1. Use a tweezers and a hammer or angle grinder to remove the floating surface of the concrete surface.
2. Remove the deteriorated concrete, expose the concrete structural layer, and repair the surface with epoxy resin mortar.
3. The surface of the concrete to be affixed is polished with an angle grinder to remove impurities such as surface floats and oil stains until the new surface of the concrete structure is completely exposed. The corners of the beam are to be angled and polished into arcs. The radius is not less than 20mm.
1-member structure layer 2-carbon fiber cloth
Paste diagram of the corner of the component
4. The concrete surface must be flat, solid, free of impurities and dry.
1-1-2-2 brushing the underlying resin
1. The base resin should be formulated in accordance with the process specifications provided by the product supplier.
2. Apply the primer resin evenly to the concrete surface using a roller brush. The next step of the construction should be carried out immediately after the surface of the underlying resin is dry.
1-1-2-3 leveling
1. According to the design requirements, the concrete carbonization and the missing parts of the beam are treated.
2. Prepare the leveling material according to the process specifications provided by the product supplier.
3. The concave part of the concrete surface should be filled with leveling material according to the design requirements, and there should be no corners.
4. Apply the leveling material at the corner and repair it with a corner grinder to make it a smooth arc with a radius of not less than 20mm.
5. Perform the next step of the construction immediately after the surface of the leveling material is dry.
1-1-2-4 paste carbon fiber sheet
1. Cut the carbon fiber cloth to the size required by the design.
2. Adjusting the glue: Calculate the dosage according to the bonded area. Accurately weigh the components A and B. According to the mixing ratio of A: B = 3:1, stir well in a clean container.
3. Use a hard brush to evenly apply the adhesive to the bonding surface. The amount of glue must be sufficient and full.
4. Apply the cut carbon fiber cloth to the concrete surface and press it with the special roller in the direction of the fiber to make the carbon fiber cloth stretch straight and the adhesive is fully penetrated. Do not damage the carbon fiber cloth when rolling.
5. Apply a part of the adhesive to the surface of the carbon fiber cloth, continue to reciprocate the scraping and rolling, remove the air bubbles, and evenly cover the carbon cloth with the adhesive.
6. Set the net for 1 to 2 hours to dry, repeat rolling to eliminate bubbles caused by fiber floating and misalignment, and false bonding.
7. Multi-layer paste Repeat the above steps, and paste the next layer after the fiber surface is impregnated with the resin finger.
8. Apply the impregnating resin evenly to the surface of the last layer of carbon fiber cloth.
1-1-5 inspection and acceptance
1. Before starting construction, the product quality certificate and product quality inspection report of carbon fiber sheet and supporting resin bonding material should be confirmed. The performance indexes should meet the requirements stipulated in the Technical Specification for Carbon Fiber Sheet Reinforcement and Restoration Concrete Structure.
2. When the concrete structure is strengthened and repaired by carbon fiber sheet and supporting resin bonding materials, the concealed engineering inspection and acceptance of each process shall be strictly carried out.
3. The actual bonding area of ​​the carbon fiber sheet should be no less than the design amount, and the position deviation should be no more than 10mm.
4. The bonding quality between the carbon fiber sheet and the concrete can be checked by tapping with a small hammer or by hand pressing the surface of the carbon fiber sheet. The total effective bonding area should not be lower than 95%. When the empty area of ​​the carbon fiber cloth is less than 10000 mm 2 , it can be remedied by means of needle injection. When the empty drum area is more than 10000mm2, the carbon fiber sheet at the hollow drum should be cut off, and the same amount of carbon fiber sheet should be lapped and attached, and the arch length should be no less than 100mm.
1-1-6 test requirements (carbon fiber cloth)
1. Test conditions
The test environment should be maintained at a temperature of 23 ± 10 ° C and a relative temperature of 60% - 70%.
2. Test steps
The sample was placed in a jig of a tensile tester and loaded at a speed of 1500-2000 N/min until it was destroyed.
3. Results
Concrete damage, construction quality is qualified, other damages meet the requirements of the positive tensile bond strength is not less than 2.5MPa, and the minimum tensile bond strength of a single sample is not less than 2.25M / Pa, the construction quality is qualified.
4. Sampling rules
According to the actual rules, the surface area of ​​the reinforcing structure of the carbon fiber sheet is pasted, a set of samples is taken for the project below 500 m2, two sets of samples are taken for the project from 500 m2 to 1000 m2, and the sample of the quilt is taken every 1000 m2 for the project above 1000 m2. The sample shall be randomly selected by the inspector and the distance between the samples shall not be less than 500mm.
1-1-7 Precautions during construction
1. The amount of one-time agitation of carbon fiber adhesive should meet the usage of this construction. It should not be exceeded. If it exceeds the use time, the adhesive should be discarded and not allowed to be used again. The effective time for sticking the glue at room temperature is usually 1 hour.
2. The bending of the carbon fiber sheet along the vertical direction of the carbon fiber filament should be avoided during the construction process.
3. During the construction, please keep the resin and colloid in a well-ventilated place, and ensure that it does not come into contact with other unidentified liquids to prevent the chemical reaction from causing the resin or colloid to fail.
1-1-8 quality assurance measures
1. When affixing carbon fiber reinforcement, the decoration surface layer must be cleaned to expose the structure itself. The carbon fiber sheet should be affixed tightly to ensure that it works synchronously with the structure.
2. The construction project changes shall be subject to the written notice of the design unit.
3. Carry out construction in strict accordance with the process quality procedures to ensure construction quality.
1-1-9 safety measures
1. The distribution box in the construction site is strictly forbidden to be used by any non-professional electrician to prevent electric shock.
2. The carbon fiber sheet is a conductive material. When constructing the carbon fiber sheet, keep away from electrical equipment and power supply, or take reliable protective measures.
3. The raw materials of the carbon fiber sheet supporting resin should be sealed and stored, away from fire sources and avoid direct sunlight.
4. The resin should be well ventilated in the place where it is formulated and used.
5. When performing beam and plate grinding indoors, the operator must take appropriate protective measures. Such as: tie the collar, sleeve collar, bring a mask and so on.
6. Keep an eye on the safety of your feet and the working environment. The scaffolding board requires that the paving and the shelf tube are firmly tied, and the probe board and the hanging board are strictly prohibited.
1-1-10 fire fighting measures
1. Smoking is strictly prohibited at the construction site.
2. On-site production and daily use of fire shall be approved by the relevant leaders, and no one shall be allowed to use open flames without authorization. Open fire operations must have safety protection, oxygen cylinder shockproof sunscreen and acetylene tanks to prevent tempering.
3. There should be sufficient fire-fighting equipment at the construction site. When using an open flame, special personnel must be taken care of and kept away from inflammable materials.
Http://news.chinawj.com.cn
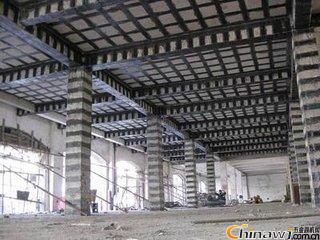
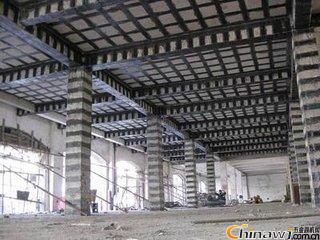
Black metal industry standard of the People's Republic of China: Ultra High Power Graphite Electrode (YB/T 4090-2000) "regulation of the ultra High Power Graphite Electrode shape, size and allow deviation, technical requirements, test methods, inspection rule, packing, marking, storage, transportation and quality certificate. It is applicable to high - power Graphite Electrode, which is made of high quality needle coke as the main raw material, which is made of molding, roasting, impregnating, graphitization and machining.
Graphite is very common in nature, and graphene is the intensity of the highest substance known to mankind, but scientists could still take several years or even decades, to find a way to graphite into a large high quality graphene "thin film" method, thus they can be used to manufacture all kinds of useful material for mankind. According to scientists, graphene in addition to very strong, but also has a series of unique features, graphene or conductive performance of the best known materials, which makes it also has great potential applications in the field of microelectronics. The researchers even see graphene as a substitute for silicon that can be used to produce future supercomputers.
superiority
1: the increasing complexity of the geometry of the mould and the diversification of the product application result in the higher and higher demand for the discharge accuracy of the spark machine. The advantage of graphite electrode is that it is easy to process, high removal rate and low graphite loss. Therefore, some of the group spark machine customers have abandoned copper electrode instead of graphite electrode. In addition, some special shaped electrode can't made of copper, but easier to forming, graphite and copper electrode is heavier, not suitable for processing large electrode, these factors have caused part of the group of the graphite electrode spark machine customer applications.
2. Graphite electrode is easier to process, and the machining speed is obviously faster than that of copper electrode. For example, graphite is processed by milling process, and its processing speed is 2~3 times faster than that of other metals, and no additional manual processing is required, while the copper electrode needs to be worn by hand. Similarly, if you use a high speed graphite processing center to make the electrode, it will be faster, more efficient, and will not produce dust problems. In these processes, selecting the right tools and graphite can reduce the abrasion loss of the cutter and the breakage of the copper gong. If the concrete is the milling time of graphite electrode copper electrode and graphite electrode, graphite 67% faster than copper electrode, in the general case of electro discharge machining, the adoption of graphite electrode machining 58% faster than using copper electrode. In this way, the processing time is greatly reduced and the manufacturing costs are reduced.
3: the graphite electrode is different from the traditional copper electrode design. Many mold factory in copper electrode roughing and finishing usually have different requirements, and graphite electrode is used almost the same amount of reserve, this reduces the CAD/CAM and the frequency of machine, sheet is for this reason, to a large extent is enough to improve the precision of the mold cavity.
Of course, the first thing that should be clear is how to use graphite materials and other related factors after the copper electrode is transferred to graphite electrode. Today, some group spark machine customers use graphite for electrode discharge machining, which is exempt from the process of mold cavity polishing and chemical polishing, but still achieve the desired surface finish. If the process of time and polishing is not increased, it is impossible for the copper electrode to produce such an artifact. In addition, the graphite is divided into different levels, and in particular the application of using the appropriate level of graphite and spark discharge parameters to achieve the ideal processing effect, if in the use of graphite electrode spark machine operators use the same as the copper electrode parameters, then the result is certainly disappointing. If the material of the electrode is strictly controlled, the graphite electrode can be used in the non-loss condition (less than 1%), but the copper electrode is not used.
Ultra High Power Graphite Electrode
Ultra High Power Graphite Electrode,Conductive Graphite,Mesh Graphite Electrode,Special Graphite Electrodes
Fengcheng Ruixing Carbon Products Co., Ltd , http://www.lnfcrxts.com