[Principles and Characteristics of Mechanical Seals and Material Selection]
1. Working Principle of Mechanical Seals
A mechanical seal is a type of shaft seal that prevents leakage by using one or more pairs of end faces that slide relative to the shaft. These end faces are pressed together under the influence of fluid pressure and the elastic force (or magnetic force) from a compensating mechanism, ensuring a tight seal. This design allows for a thin liquid film between the sealing surfaces, which helps in lubrication and pressure balance, making it ideal for high-performance applications.
2. Selection of Common Materials for Mechanical Seals
For clean water at normal temperature:
- Moving ring: 9Cr18, 1Cr13 with cobalt-chrome-tungsten overlay
- Stationary ring: Resin-impregnated graphite, bronze, phenolic plastic
For river water (with sediment) at normal temperature:
- Moving ring: Tungsten carbide
- Stationary ring: Tungsten carbide
For superheated water (100°C):
- Moving ring: Tungsten carbide, 1Cr13 with cobalt-chrome-tungsten overlay
- Stationary ring: Resin-impregnated graphite, tungsten carbide, cermet
For gasoline, lubricating oil, and liquid hydrocarbons at room temperature:
- Moving ring: Tungsten carbide, 1Cr13 with cobalt-chrome-tungsten overlay
- Stationary ring: Resin-impregnated or tin-bismuth alloy graphite, phenolic plastic
For gasoline, lubricating oil, and liquid hydrocarbons at 100°C:
- Moving ring: Tungsten carbide, 1Cr13 with cobalt-chrome-tungsten overlay
- Stationary ring: Bronze or resin-impregnated graphite
For media containing particles:
- Moving ring: Tungsten carbide
- Stationary ring: Tungsten carbide
3. Types and Uses of Sealing Materials
Sealing materials must meet various functional requirements depending on the media and working conditions. Key characteristics include:
- Good compactness to prevent leakage
- Proper mechanical strength and hardness
- Good compressibility and resilience
- Resistance to high and low temperatures
- Excellent corrosion resistance
- Low friction coefficient and good wear resistance
- Ability to conform to the sealing surface
- Long aging resistance and durability
- Easy to process and cost-effective
Common sealing materials include rubber, graphite, PTFE, and various sealants. Each material is selected based on the application's specific needs.
4. Technical Essentials for Installation and Use of Mechanical Seals
- Ensure radial runout of the shaft is ≤0.04 mm and axial play ≤0.1 mm
- Keep the sealing area clean during installation
- Avoid knocking or hitting during installation
- Apply a thin layer of mechanical oil to contact surfaces
- Ensure even tightening when installing the static ring
- Test the moving ring for flexibility and elasticity
- Fill the equipment with medium before operation to avoid dry friction
- For high-temperature or particulate media, use flushing and cooling systems
- Choose the right mechanical oil to avoid premature failure
5. The Three Sealing Points of Mechanical Shaft Seals and Their Principles
The three sealing points include:
- The interface between the rotating and stationary rings
- The dynamic seal between the rotating ring and the shaft
- The static seal between the stationary ring and the housing
The primary sealing point is between the rotating and stationary rings, where spring or bellows pressure maintains contact, creating a thin liquid film for lubrication and pressure balance. The other two points ensure the entire system remains sealed against external contaminants and internal leakage.
6. Types of Mechanical Sealing Technology
Modern mechanical seals incorporate advanced technologies such as slotted sealing, zero-leakage, and gas-sealing methods. These technologies improve performance, reduce wear, and enhance reliability.
- Slotted sealing technology creates hydrodynamic effects through grooves on the sealing face
- Zero-leakage seals minimize or eliminate leakage
- Dry-run gas seals operate without liquid lubrication
- Thermal fluid dynamic sealing uses heat-induced pressure for better performance
- Bellows seals provide flexible compression
- Multi-face seals offer additional layers of protection
7. Mechanical Seal Flushing Programs and Features
Flushing is essential for maintaining seal integrity. It removes impurities, prevents air pockets, and improves lubrication. Common methods include internal and external flushing.
- Internal flushing uses the process fluid to clean the seal
- External flushing introduces compatible cleaning fluids from an external source
- Full flushing recirculates the fluid for better cooling
The choice of flushing method depends on the operating conditions, including temperature, pressure, and media type. Proper flow rate and pressure control are crucial for effective sealing.
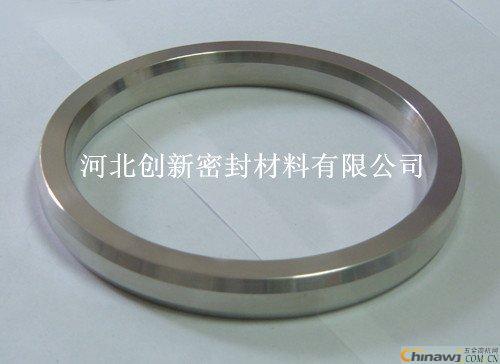
Flange housing also known as Flange Bearing Housing.
Flange housing/ Flange bearing housing is a commonly used blocks in manufacturing, mining, and construction industries for mounting self-aligning ball or spherical roller bearings with adapter sleeves or cylindrical bores. They are designed for use on conveyors, dryers, road building equipment, run-out tables, fans, crushers, hammer mills, and many other high-precision, heavy duty applications.
SHAOXING QIFENG AUTO PARTS CO., LTD (QFAP) have specialized in producing US/EURO standard bearing housings more than 10 years, could help to design the bearing housing or produce the bearing housing according to your requirements. (OEM accepted)
Materials: Ductile iron, Grey iron, Steel Castings
Surface treatment: painting, powder coating, zinc plating, only oiled
Main of our customers is from USA, CANADA, AUSTRALIA and German
Flange Blocks,Flange Block Bearing,Wooden Flange Blocks,Designed Flange Blocks
SHAOXING QIFENG AUTO PARTS CO., LTD. , https://www.sxqfap.com