Our company has undertaken the task of ion nitriding on the inner ring gear surface of a large mine car reducer. The ring gear (see photo) is a special double-connected, thin-walled structure and requires a high precision level. The left end module is 11.7 and the right end. The modulus is 8.7 and the material is 40CrNiMo. Nitrogen is the last step of the gear due to the process of nitriding after grinding the finished product. To ensure the high-precision level of the gear, it is necessary to strictly control the nitriding deformation. In actual production, the distortion after nitriding has always been a problem that plagues domestic and foreign heat treatment production. Once the deformation can not be effectively controlled, the accuracy level of the gear is reduced, and the entire gear transmission system generates impact vibration and noise during operation, which reduces the reliability of operation and affects the life of the whole machine. Through the process innovation and experimental verification, the problem of nitriding deformation of the ring gear is basically solved.
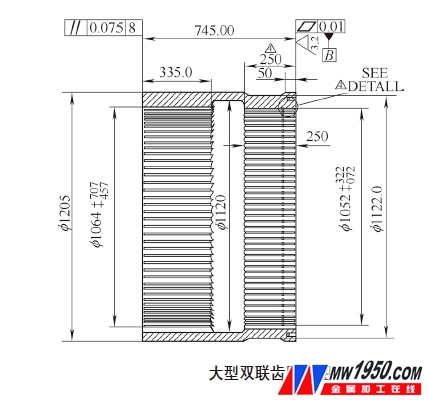
1. Large double ring gear material process
The chemical composition of the ring gear is shown in Table 1.
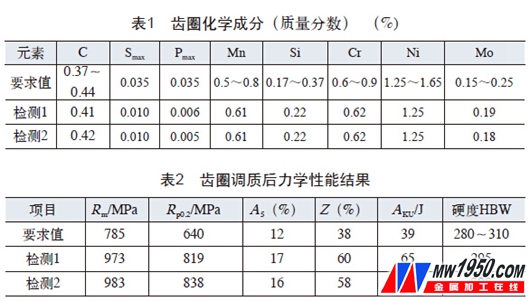
(1) Technical requirements Tempering hardness 280 ~ 310HBW. The nitriding layer is 0.3-0.5 mm deep, the white bright layer is <0.01 mm, and the surface hardness is 53.5 HRC (the surface hardness of the test piece of HR15N).
(2) Processing process The main processes of the ring gear: forging → normalizing → quenching and tempering → vertical car → inserting teeth → annealing → vertical car → inserting teeth → vertical grinding → stable aging → grinding teeth → nitriding → finished product inspection.
Conventional heat treatment process: normalizing treatment in forging factory; quenching and tempering process is (850±10) °C×(3~4)h, oil cooling; annealing process is (530±10)°C×(3~4)h, furnace cooling The nitriding process is (510 ± 10) ° C × (10 ~ 12) h, and the furnace is cooled.
Innovative process: The normalizing process is (880±10) °C × (3 ~ 4) h, air cooling; the quenching and tempering process is (850 ± 10) ° C × (3 ~ 4) h, water quenching oil cooling; annealing process is ( 530±10)°C×(3~4)h, furnace cooling, lifting temperature ≤50°C/h; stable aging process is (510±10)°C×( 3 ~ 4 ) h , furnace cooling, lifting temperature ≤ 2 5 °C / h ; The nitriding process is (510 ± 10) ° C × (10 ~ 12) h, furnace cooling, temperature rise and fall speed ≤ 25 ° C / h, improved furnace mode, auxiliary heating device.
2. Test results
(1) Mechanical properties The left end of the ring gear is raised by 50mm after cutting. The mechanical properties of the ring gear produced by the water quenching oil cooling process meet the requirements, as shown in Table 2.
(2) Deformation after annealing After the rough opening, the stress on the surface of the part due to processing is large, and the stress relief annealing process needs to be added. In order to control the deformation caused by subsequent nitriding, it is necessary to strictly control the temperature rise and fall and the holding temperature. The deformation was detected after annealing, and the ellipticity was 0.05 mm.
(3) After the aging treatment, the deformation detects the coarse grinding teeth, the parts still produce machining stress, and also need to be annealed. If it is annealed in a common electric furnace, the surface will be slightly oxidized, which will affect the nitriding effect, so it is aged in the nitriding furnace. Advantages: further eliminate processing stress; detect deformation, prepare for the next processing; test whether the nitriding tooling and tire loading method are reasonable. The deformation before and after aging is shown in Tables 3 and 4.
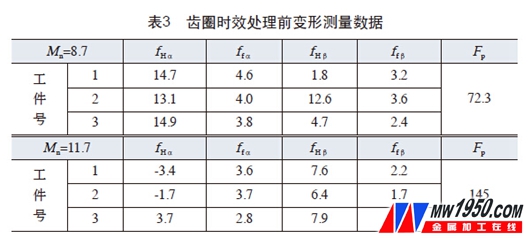
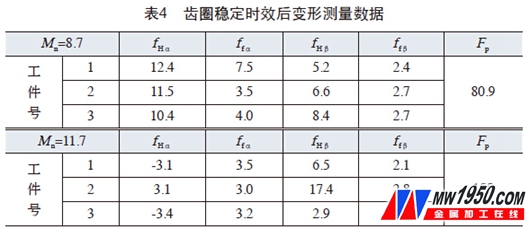
Before and after the stable aging, the deviation of the tooth profile tilt (f Hα), the tooth profile deviation (ff α), the helix tilt deviation (f Hβ), the spiral shape deviation, etc. (f fβ), the accuracy level is less than At 7th level, the cumulative total deviation of the pitch is up to (F p) to 9 levels of accuracy. It shows that there is a certain deformation in the diameter direction of the ring gear, and the diameter of the ring gear is increased by 0.15 mm.
(4) Detection of nitriding deformation The three-coordinate detecting device is used to detect the deformation of the ring gear. The specific data is shown in Table 5.
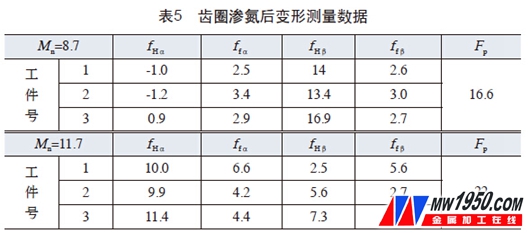
3. Analysis of factors affecting deformation
(1) Tempering and quenching The quenching process is changed from oil cooling to water quenching and oil cooling. The advantages of subsequent control deformation are: 1 increase the depth of the hardened layer of the ring gear, adopt the oil cooling process, and the hobbing rear ring gear only has a part of the tooth top. In the hardened layer, the water quenching oil cooling process is adopted, and the tooth top and the tooth root of the hobbing rear ring gear are in the hardened layer, and the deformation amount due to the difference in the structure is reduced. 2 Improve the hardness of the core of the ring gear, and improve the high temperature plastic deformation resistance of the material. 3 Improve the tempering temperature and eliminate the stress.
(2) Annealing and stable aging Add a stable aging treatment before the grinding of the teeth to reduce the machining stress generated by the gear teeth and coarse grinding teeth. Stress relief annealing creates two favorable conditions: 1 low heating temperature and low thermal stress. 2 The heating rate is slow and the temperature gradient is small. Both of these points are beneficial for the stress release and the distortion of the lattice recovery process, so that the deformation is reduced.
(3) In the initial stage of ion nitriding, the temperature difference existing in each part is large, and the generated thermal stress is enough to cause the deformation of the part that reaches the high temperature first. The heating rate and ammonia flow rate are also important factors affecting the quality of nitriding. Control the temperature rise and temperature drop rate of nitriding ≤25 °C / h, increase the auxiliary heating device, improve the heating uniformity of each part of the ring gear, and avoid the deformation caused by the thermal stress caused by the temperature difference.
4. Conclusion
(1) After adjusting the cold working process, improving the preliminary heat treatment method, eliminating the stress mode, using the innovative nitriding process, the strength of the ring gear base is improved, and the distortion of the ion nitriding ring gear becomes effective control.
(2) According to the data analysis, there is still some fluctuation in the total deviation of the pitch (F p), which needs further study.
About the author: Chen Fengyan, Zhang Changqing, Cao Fengjiao, Liu Jun, Dalian Huarui Heavy Industry Group Co., Ltd. Reducer Factory.
E27 Led Bulb,Led Bulb Lamp,Led Lamp Light,Dimmable Led Light Bulbs
Guangdong Smart Street Lighting Co., Ltd , https://www.fldlight.com