There are five methods for industrially producing acrylic acid, namely, a propylene oxidation method, a modified Reppe method, an acrylonitrile hydrolysis method, a cyanide method, and an enone method. These methods have been used as the main method for producing acrylic acid and esters. The latter two methods have been eliminated due to their low efficiency and high consumption. The acrylonitrile hydrolysis method is limited to the production of MA and EA. When producing higher esters, further transesterification is required. The improved Reppe method once dominated the development of coal chemical industry. Some companies still use the acrylonitrile hydrolysis method and the improved Reppe method. However, in recent years, the new equipment in the world has tended to adopt the advanced process, low cost and high efficiency of propylene oxidation.
The propylene oxidation process is divided into a one-step process and a two-step process. However, due to the inherent shortcomings of the one-step process, there is no possibility of industrialization. The two-step process makes each oxidation reaction optimal and is the most economical process. The first step oxidizes propylene to acrolein; the second step further oxidizes acrolein to acrylic acid. At present, the world's propylene oxidation process acrylic technology mainly includes the United States Sohoo (Sohio) technology, Japan Coal Touch Technology (NSKK), BASF technology, Japan Mitsubishi Chemical Technology (MCC).
Progress in the production of acrylates from acrylic stadiums
The former US Soho (Sohio) is now owned by a part of BP. In the 1960s and early 1970s, Sohio and BASF technology had many industrial installations in the United States and Japan. However, in the 1980s, the production equipment originally using Sohio and BASF technology was replaced or partially replaced by NSKK and MCC technology. Instead, catalysts such as the Sohio process have used NSKK. At present, the technology of NSKK and MCC companies has come to the fore. Its technical advantages lies in reasonable process and excellent catalyst performance, which makes the final reaction have good selectivity and high yield of acrylic acid.
The technical level of AA's two-step oxidation process depends mainly on the performance of the catalyst, which is the key to AA production. The catalysts of Nippon Catalyst Chemical and Mitsubishi Chemical Corporation have good activity, long service life and high mechanical strength, so the two companies Technology is at the leading edge. It is said that the MCC catalyst has undergone major improvements in recent years.
1. Sohio technology In the late 1960s and early 1970s, there was a certain market in the United States and Japan. At present, only two sets of devices use this technology, with a capacity of 140,000 tons/year, accounting for 5.66% of the world's total capacity; acrylate production capacity is 132,500 tons/year, accounting for 6.71%-6.48% of the world's total capacity. Sohio technology has not improved much since the 1970s. It is characterized in that propylene oxidation is operated in series by two reactors, the exhaust gas from the top of the absorption tower is not recycled; the unreacted propylene in the exhaust gas is not recovered; the catalyst life is two years; and the three ester-type esterification reactors are used for methyl and ethyl esters. Continuous production; butyl ester uses a production line, three reactors are operated continuously in series, using H2SO4 as a catalyst.
2. BASF Technology BASF is one of the world's largest acrylic and ester production plants. In addition to retaining a modified Reppe process, it built 250,000 tons of acrylic acid and 200,000 tons of ester in Ludwigshafen. Class equipment; 136,000 tons of acrylic acid and 159,000 tons of ester equipment were built in the United States, and 160,000 tons/year of acrylic acid and ester were newly built in 1996.
Features of BASF propylene oxidation technology:
1 The two-stage oxidation method of propylene fixed bed is adopted, and the propylene oxidation reaction gas is not absorbed by water, but is absorbed by a selective organic solvent. After separation and refining by three columns, esterification grade and polymerization grade acrylic acid can be obtained, the process is simple, and almost no waste water is produced in the acrylic acid synthesis part.
2Ma, EA reaction does not use an ion exchange resin bed, but a reaction tower using H2SO4 as a catalyst. In addition, the recycle gas and fresh air are separately compressed by two compressors.
3. Japan's Mitsubishi Oil Chemical (MPCL) Technology The company developed the propylene vapor phase oxidation acrylic technology in 1962; in 1973, the first industrial production plant was established in Yokkaichi, Mie Prefecture, Japan. Set, accounting for 457,200 tons / year of acrylic acid, esters of 329,000 tons / year.
Features of MPCL technology:
1 The propylene concentration required for the oxidation reaction is low, and 95% by mol of propylene can be used.
2 has a higher propylene conversion rate and acrylic acid yield, a reaction propylene conversion rate of 98%, a two-stage reaction propylene, aldehyde conversion rate of 99.3%, a total conversion rate of 98%, and a total acrylic acid yield of 88%. .
3 Propylene oxidant has a long service life, and the catalyst life of one-stage and two-stage reaction is more than 6 years.
4 Adopt "one pass" oxidation reaction technology. Due to the high conversion of propylene, the reaction off-gas does not need to be recycled.
5 pairs of the first and second stage reactors are introduced into the air to increase the propylene feed concentration from 6% to 10%, reduce the steam amount and energy consumption, and make the acrylic acid concentration in the acrylic quench tower from the original 32 The % is increased to 50%, reducing the load on the refining system and the amount of wastewater discharged.
6 Acrylic refining system changed from five towers to three towers, reducing equipment investment costs.
7 can produce high quality acrylic acid, even under the condition of using low purity propylene, the purity of acrylic acid can be greater than 99.8%.
8 butyl acrylate production is a continuous production process using organic acid as a catalyst, using a six-tower separation and purification system.
4. Japan Catalyst Chemistry (NSKK) Technology The company's research on the oxidation of propylene to acrylic acid began in 1960. The first industrialized unit was built in 1970. The company has established three industrial units with its own technology at its Himeji factory. At present, 17 sets of devices have been built, rebuilt, expanded and newly built using NSKIC technology, with a total of 1.476 million tons/year and 1,292,200 tons/year of esters.
The characteristics of NSKK technology are:
1The propylene oxidation reactor is changed from two series to one superimposed tubular reactor, using a heat dissipation system of inorganic heat medium, and the reactor material is changed from the original 304 stainless steel to carbon steel, which simplifies the process and saves The investment.
2 has a higher catalyst life, a period of catalyst life of 8 years.
3 The gas composition of the inlet of the reactor, the propylene concentration is increased from the original 6.5% (volume percent) to 7% (volume percent), and the water vapor concentration is reduced from 10% to 7%, so that the concentration of the aqueous solution of the absorption bottom acrylic acid is 40.97% ( Wt) increased to 65% (wt), reducing wastewater.
The yield of 4 acrylic acid increased from 86% to 87% (mol).
5 The 40% oxidation reaction waste gas cycle not only improves the conversion of propylene, but also provides water vapor for the reaction gas without adding fresh steam.
The 6 aqueous acrylic acid solution was changed from extractive distillation to azeotropic distillation, shortening the process. The refining system was changed from the original nine towers to five towers, reducing the consumption of public works.
7 butyl acrylate was changed from batch production with H2SO4 as catalyst to continuous production process with ion exchange resin as catalyst, which reduced separation equipment, wastewater discharge and acid and alkali pollutants.
8 Exhaust gas catalytic incinerator is used, no fuel gas is consumed.
In recent years, various acrylic acid producers in the world have developed new process technologies to varying degrees and entered the international market competition with their respective advantages. Currently, MPCL and NSKK are the most active. The production of acrylates includes methyl acrylate, ethyl ester, butyl ester and octyl ester. Although the varieties are different, the production methods are similar, and the esterification reaction of acrylic acid with the corresponding alcohol is used.
At present, the global market for (meth)acrylic acid and esters has expanded from the early years of technologically advanced countries and regions (US, Japan, and Western Europe) to cover sub-technical development, underdeveloped technology, and developing countries. It is not obvious. Production facilities are installed in Brazil, Canada, Mexico, Europe, Czech Republic, the Netherlands, the United Kingdom, Italy, Russia, Asia, Malaysia, Singapore, Thailand, Indonesia, and India. (Meth)acrylic acid and ester or polymer products are traded and traded in many countries and regions around the world.
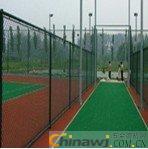
Aluminum Casting Led Lighting Parts
Aluminum Casting Led Lighting Parts,Led Bulb Aluminum Housing,Led Aluminum Extrusion,Led Aluminum Profile
NINGBO AIKEHAN METAL PRODUCT CO.,LTD , http://www.diecastingsupplier.com